RS PRO Hybrid, Permanent Magnet Stepper Motor 0.9°, 0.36Nm, 2.8 V, 1.68 A, 4 Wires
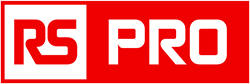
Technical Document
Specifications
Product details
0.9° and 1.8° Hybrid Stepper Motors
1.8° Step Angle,The motors are directly compatible with the stepper motor drive boards and also drive either motor (if required) in the half step mode i.e. 0.9° per step resulting in higher resolution, greater performance stability and faster stepping rates. Direction, velocity, acceleration/deceleration can be controlled by a stepper motor controller.,Applying the correct electrical pulse sequence to the windings of the stepper motor results in a 1.8° step angle rotation of the spindle (i.e. 200 steps per revolution). When correctly loaded and driven these motors will produce discrete output steps. The number of steps and speed of rotation are determined by the number of pulses and frequency of the input signal. This provides an ideal method for speed and position control. The motors are directly compatible with stepper motor drive boards.,Applications include:
P.O.A.
1
P.O.A.
1
Stock information temporarily unavailable.
Please check again later.
Technical Document
Specifications
Product details
0.9° and 1.8° Hybrid Stepper Motors
1.8° Step Angle,The motors are directly compatible with the stepper motor drive boards and also drive either motor (if required) in the half step mode i.e. 0.9° per step resulting in higher resolution, greater performance stability and faster stepping rates. Direction, velocity, acceleration/deceleration can be controlled by a stepper motor controller.,Applying the correct electrical pulse sequence to the windings of the stepper motor results in a 1.8° step angle rotation of the spindle (i.e. 200 steps per revolution). When correctly loaded and driven these motors will produce discrete output steps. The number of steps and speed of rotation are determined by the number of pulses and frequency of the input signal. This provides an ideal method for speed and position control. The motors are directly compatible with stepper motor drive boards.,Applications include: